Experts reveal critical skills & job roles for the future of manufacturing
.png)
- Leadership, sales and communication are the most sought-after skills in manufacturing, vital for driving innovation, talent retention, and collaboration in a globalized market.
- With a shift towards consultative sales approaches, manufacturing sales teams are being trained to identify customer pain points, articulate value propositions, and manage complex sales pipelines for new products.
- The rapid evolution of technology has created demand for specialized roles to drive efficiency, security, and innovation.
The manufacturing industry is undergoing intense transformation. From electrification and supply chain disruption to rising market competition, staying ahead of change is becoming increasingly challenging.
To cope with these challenges, manufacturers are not only pivoting their technology strategies, but also their workforce development. By aligning industry and market trends with their people’s upskilling, global manufacturers are able to thrive in disruption and strengthen their market position.
In this article on the future of manufacturing, we’ll draw on expert opinions and Lepaya’s industry-specific data to:
- Analyze key trends shaping the manufacturing industry
- Identify the industry critical skill gaps and leading job roles of the future
- Train the relevant skills for emerging technologies and build a future-proof workforce
The industry trends shaping the future of manufacturing
Electrification, new AI technologies and an aging workforce demand complex change management for manufacturers. Especially in commercial and operation teams, there’s a growing need to work with new products and communicate the value to customers.
In Lepaya’s Evolution of Skills 2030 research, leading learning managers from Roxtec and Electrolux analyzed how industry advancements are impacting their teams:
“It’s the green transition and then there's a risk of more and more people retiring. AI is also influencing our operating models and putting us in situations where change will be constant. So we have to ask ourselves; how can we bring our workforce into a situation where they can thrive?”
Konstantina Held, Global Skills Manager at Electrolux Group
“New technology is a driving factor that shapes future skills, especially for the older generations in our workforce. How can we upskill our people in AI to communicate, make new products and integrate it into sales processes? There is also a higher demand for agility. We have to adapt and change faster than before.”
Patrik Gustavsson, Global L&D Manager at Roxtec
With the importance of sustainability and integrating technologies increasing, learning leaders have to find new solutions to continuously upskill every level of their global workforce - especially older generations - to be agile and adapt.
So which skills are global manufacturers training to equip their globally distributed workforce with the relevant capabilities?
The top skills in advanced manufacturing
Based on Lepaya’s research data from 84.704 hours of training, and 17.234 learners in the first 6 months of 2024, these are the top skills we uncovered in the manufacturing industry:
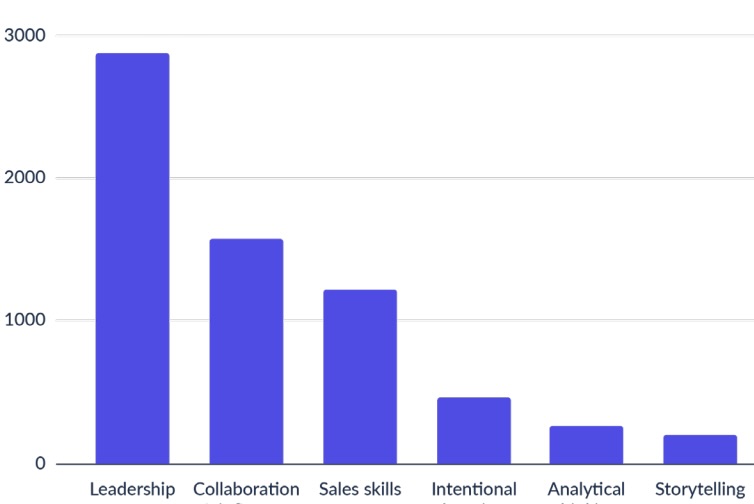
From the analysis, manufacturers are focused on three competencies to manage disruption and stay competitive in the global market; leadership, communication and commercial skills. Let's explore why they are training these skills and the impact on companies’ growth and competitiveness.
Leadership skills drive manufacturing innovation forward
As the most-trained skill, leadership accounted for nearly 3,000 hours of learning time in the first half of 2024. With intense transformation, leadership skills keep their teams working toward achieving critical business goals and improve talent retention rates.
When we break down the specific leadership skills manufacturers are training, here are the most common three:
- Giving feedback: Essential for growth and development, feedback must be actionable and clear to have the desired results in fast-changing environments.
- Handling difficult conversations: A crucial part of any leadership role in a period of transformation, difficult conversations are easier when handled with a structured approach.
- Critical decision-making: Strategies and tools can improve decision-making skills in high-pressure situations and boost business results.
Manufacturing leader Siemens, for example, is training its leaders in team collaboration, emotional intelligence and adaptability to make them fit-for-future. By establishing a “Positive Leadership Culture,” the company is developing leaders with the mindset and skills needed to empower people during change.
At the same time, they’re able to encourage innovation and stronger performance. The results are clear for manufacturers that invest in their leaders: higher productivity, revenue and above all - talent retention rates.
“Positive leadership means optimizing your resources and strengths to improve customer value and business impact.”
Sylvia Käsler, Organizational Development & Coaching at Siemens
“One of our biggest challenges in the manufacturing sector is hiring skilled talent and it’s important for us that our leaders are able to retain and develop our employees. When we lose people, we have to hire to replace them and add extra talent for support."
Patrik Gustavsson, Global L&D Manager at Roxtec
Advanced manufacturing jobs require advanced communication skills
In addition to leadership, communication skills - ranked second in 2024 - are also crucial for the long-term success of manufacturing companies. In a globalized market and complex supply chain, collaboration is important for handling cross-border business and sales.
Key communication skills trained in 2024 include:
- Active listening: Truly understanding what someone is saying requires the ability to go below the surface and ask questions that reveal the heart of the matter at hand.
- Conscious communication: Body language, emotions and relationships all play a role in communication. Knowing how they work together also makes it easier to understand others.
- Storytelling: Powerful stories communicate trust, credibility and authenticity while inspiring and motivating an audience.
“Communication skills are important for our success as a global manufacturer. Particularly in our context where we have teams - including sales and engineers - working with different countries, cultures, products and sectors.”
Patrik Gustavsson, Global L&D Manager at Roxtec
Addressing the skills gap in advanced manufacturing with sales training
In the first six months of 2024, manufacturing companies increasingly focused on sales skills to improve competitiveness - rising from 600 hours trained in 2023 to 1300.
As manufacturing sales moves towards a consultative approach - centered around understanding the needs of customers and advising on new products - salespeople need upskilling to adapt. They have to learn how to zoom in on pain points while establishing strong relationships through:
- Pipeline management: Salespeople must understand the sales pipeline and how it connects with the buyer’s decision-making process to provide guidance throughout the journey.
- Advanced value selling: Commercial teams need to go from presenting features to articulating the unique value their solution brings to clients’ challenges. This involves aligning offerings with the client’s goals, quantifying the ROI, and positioning themselves as trusted advisors.
- Uncovering the client’s situation: Understanding a client's needs is the cornerstone of success and requires understanding their unique needs and circumstances to establish a strong relationship.
“Our sales people have to pivot to work with new technologies, sell new product features and adapt to customers who are becoming more knowledgeable. Now they tend to find us, instead of us finding them.”
Patrik Gustavsson, Global L&D Manager at Roxtec
The leading job roles for the future of manufacturing
To help manufacturers identify the right skills and execute talent succession planning, anticipating future jobs - even those that don't exist yet - is critical. Lepaya’s Evolution of Skills 2030 research highlighted that as technology rapidly evolves, the demand for specialists in cyber security and AI will grow.
Here are 3 leading job roles for the future of manufacturing:
Blockchain Specialist
Blockchain specialists implement tech to enhance transparency and security within the manufacturing supply chain. By leveraging blockchain, these specialists ensure that every transaction, from raw material sourcing to final product distribution, is securely recorded and easily traceable.
This not only mitigates risks such as counterfeiting and data breaches, but also optimizes supply chain efficiency by streamlining administrative tasks and regulatory compliance.
Digital Transformation Leader
In the era of Industry 4.0, manufacturers need talent that can integrate digital tech across the production line. With the Internet of Things, AI, and data analytical skills, these leaders enhance operational agility, improve quality control processes, and drive innovation in product development.
Augmented Reality Technician
Augmented reality (AR) technicians enhance manufacturing processes through the real-time visualization of complex machinery and production workflows. This reduces machinery downtime through remote troubleshooting, allows concepts to be refined in a virtual environment before production, and boosts operational efficiency.
“In terms of specific roles that will emerge in the sector, I believe those related to AI, especially large language models and big data, will be critical. Regulatory experts who can help companies navigate new laws will also be in demand.”
Marek Spányik, Project Officer at Automotive Skills Alliance
Anticipating future skills and upskilling builds manufacturers’ resiliency
In the years to come, manufacturing companies will need to continuously upskill their people to remain competitive, adapt to technology and create new avenues for market growth.
Driven by electrification, AI, and sustainability trends,manufacturers must invest in workforce upskilling, equipping their teams with leadership, communication, and sales skills to navigate disruption and drive innovation. Preparing for the future also involves recognizing the roles emerging from technological advancements, such as blockchain specialists and augmented reality technicians, ensuring manufacturing remains agile and resilient in the face of change.
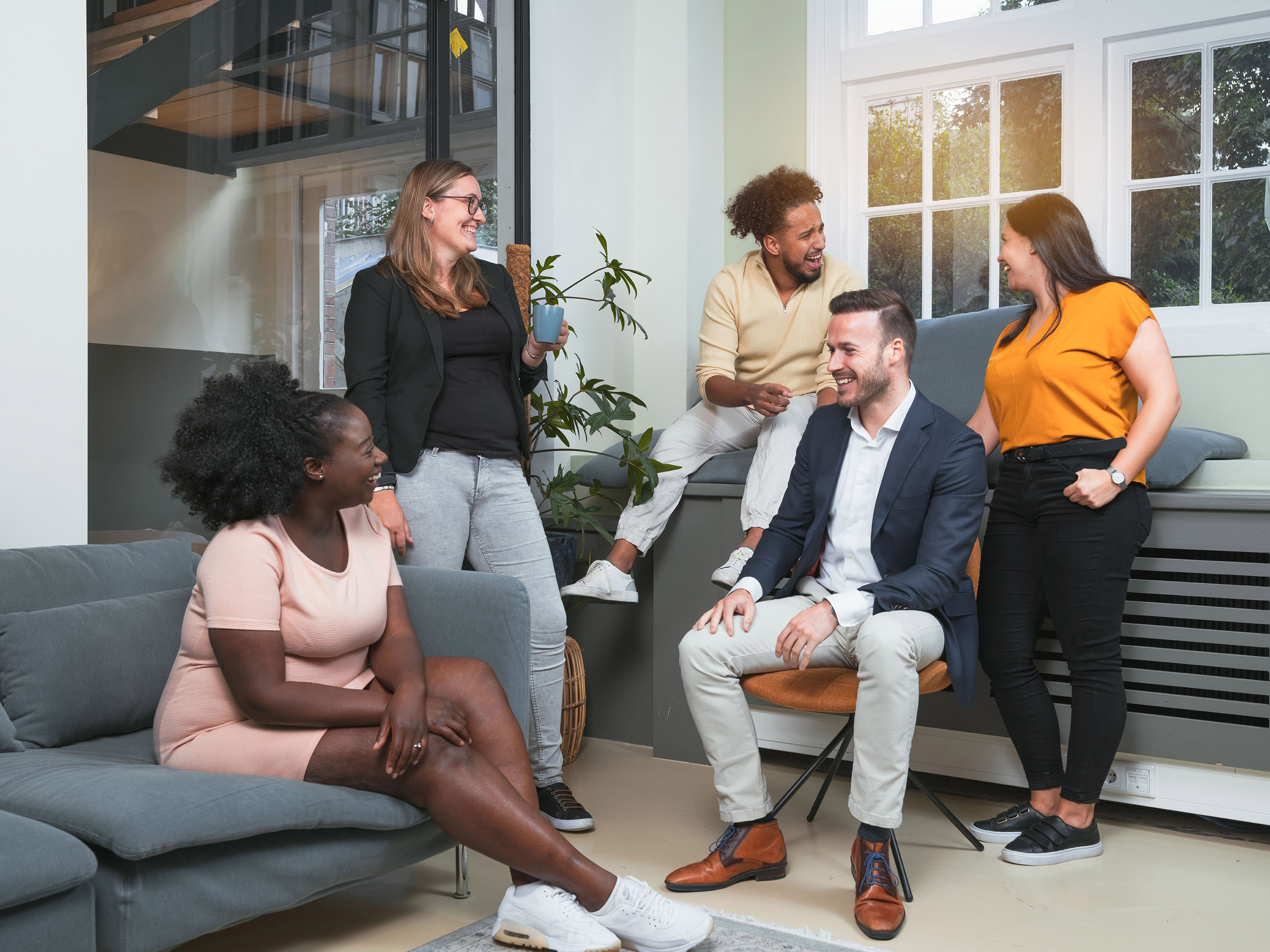
We offer a scalable employee training solution. It lets you continuously upskill your people.
Book a call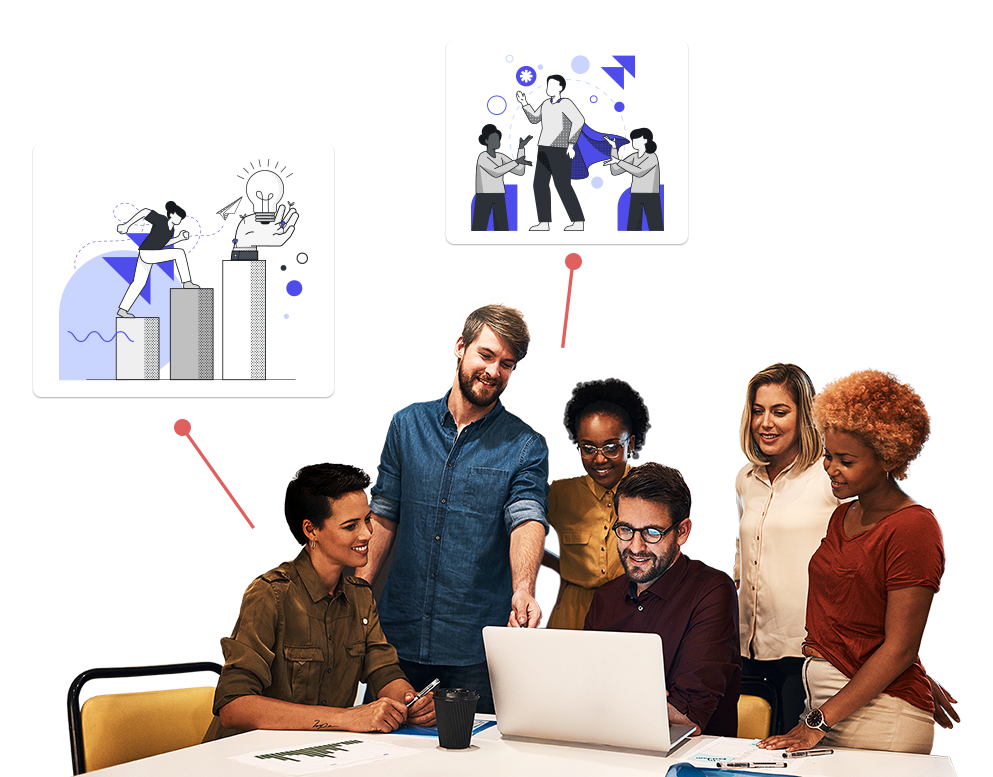
Related articles
View all posts.png)
Review by:
Marketing meets L&D: Ashley Hinchcliffe on how marketing can drive learner engagement
By adopting a marketing mindset, L&D teams can transform learner engagement by treating learning as an ongoing experience—leveraging audience insights, branding, personalization, and multi-touchpoint campaigns to capture attention, sustain participation, and drive measurable impact.