Leadership upskilling and succession planning in the manufacturing industry
.jpeg)
• Manufacturers are integrating new technology to increase operational efficiency and sustainability.
• Soft skills training is essential for talent to adapt to operational changes in automated operations.
• Talent attraction and retention are key challenges for manufacturing C-level leaders.
• Succession planning is crucial for retaining skilled talent and ensuring a consistent supply of internal expertise.
• Manufacturers need to decrease their reliance on the external market by developing in-house capabilities and leadership pipelines for successful change management in smart factories.
Manufacturers are integrating new technology into operations. Advanced production methods can forecast customer demand and increase machinery downtime to improve cost-efficiency.
However, as the industry innovates factories across the globe, supporting talent to handle change is key to retention, productivity and Return on Investment (ROI).
Manufacturers can train talent’s hard skills to comply with new safety regulations and operate machinery. But training soft skills for operational change at scale is more complex.
Why do soft skills matter in automated operations and how can manufacturers increase retention rates with talent succession planning?
Download your guide for the manufacturing industry
New technology increases operational efficiency and sustainability
Automation will decrease repetitive tasks in assembly lines and require talent to develop and maintain new technologies. With a focus on AI robotics and advanced data systems, manufacturers will not only be able to increase efficiency, but also sustainability as AI-based applications predict energy consumption and reduce emissions.
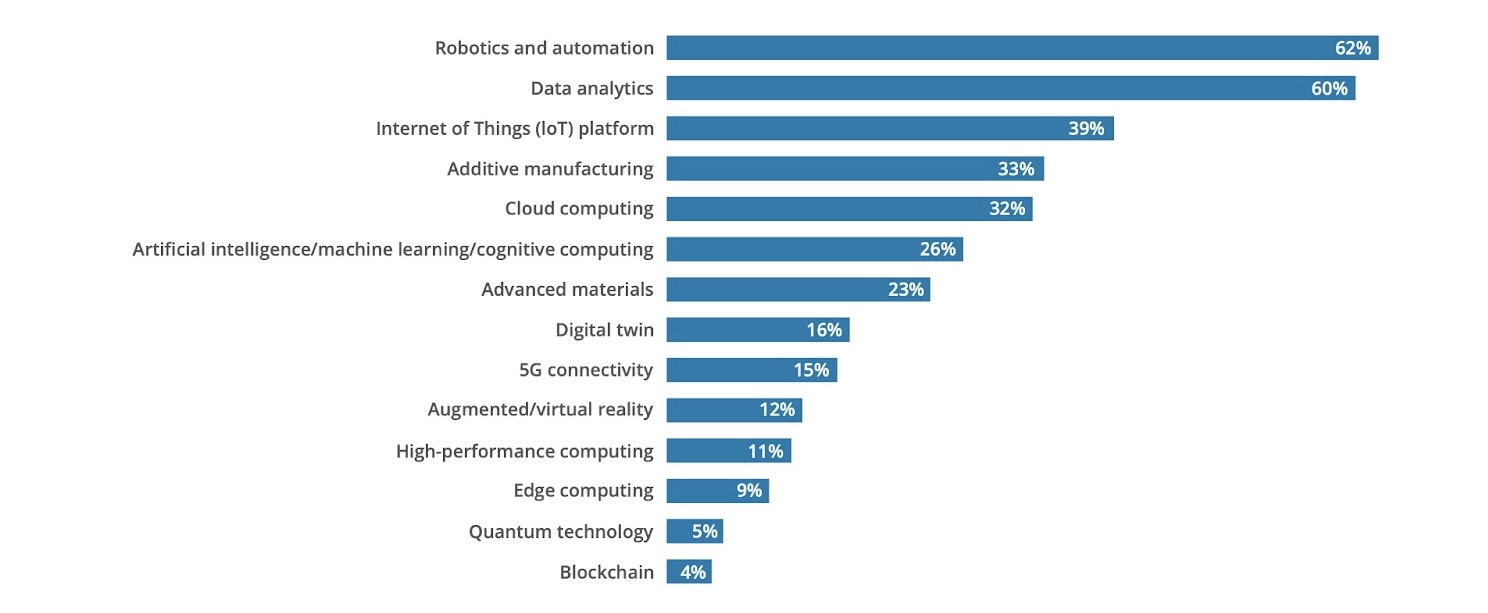
However, this technology cannot deliver monetary and sustainability value alone. Manufacturers need operation teams to adapt to new ways of working and ensure machinery produces results to justify investment.
Therefore, upskilling initiatives cannot only focus on hard skills, but they also need to support talent to adapt and succeed in high pressure environments.
Talent attraction & retention trouble manufacturing C-level leaders
Technology does not just demand a change in skills, but also access to talent resources to fill new positions in global smart factories. The top 5 challenges for managing production teams reflect C-levels' difficulty to attract and retain high-performing talent.

As manufacturers struggle to source the right talent for AI operations, they are exploring other growth avenues and solutions to transform smart factories.
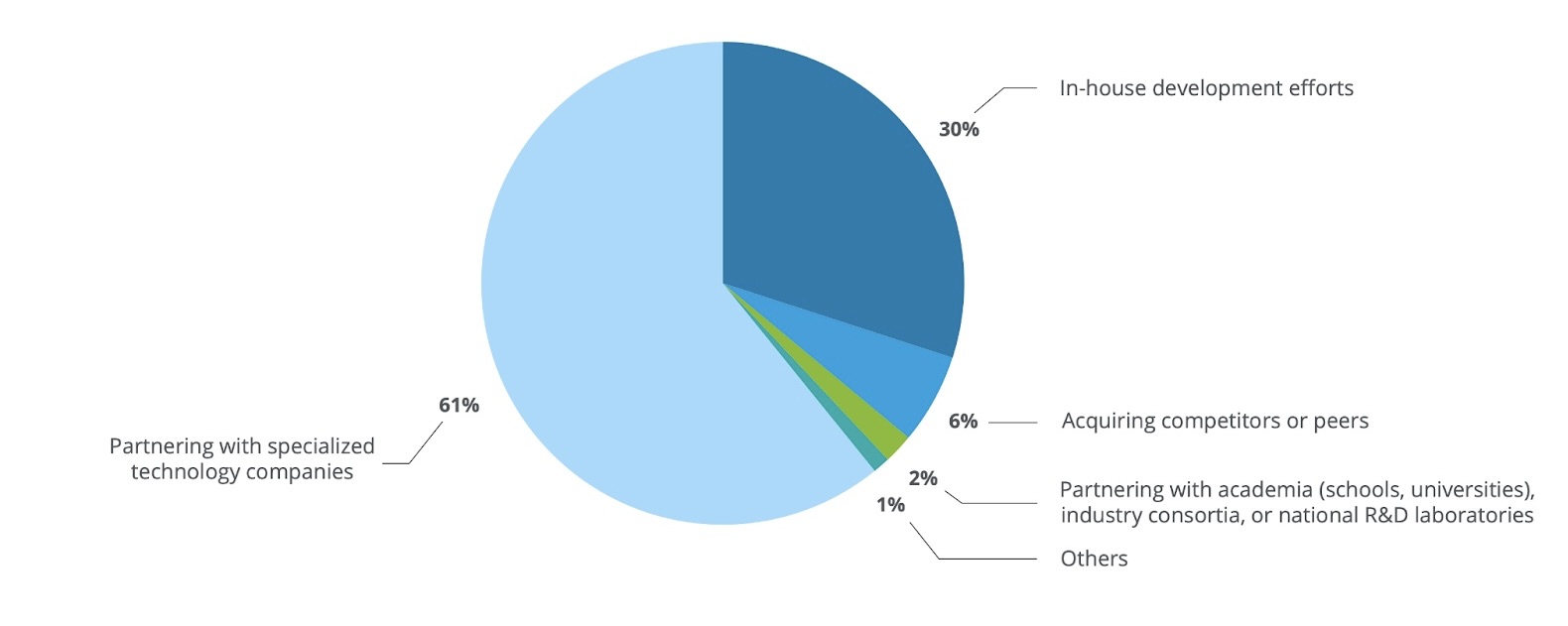
Manufacturers are dependent on a mix of external partners, acquiring competitors and in-house developments to implement AI transformation. But the dominant manufacturers who successfully integrate AI technology will rely on in-house capabilities as their primary growth source .
Once the AI is integrated, manufacturers still need skilled talent to maintain and operate machinery. Therefore, they have to develop as much in-house expertise as possible to be financially and technologically efficient.
Succession planning retains skilled talent for transformation
Manufacturers need to increase their internal development of skilled talent. Setting up upskilling programs and academies ensures a consistent supply of internal expertise. And as more smart factories are established across the globe, companies can redistribute experts and pass on their knowledge to teams in new roles.
However, manufacturers also need solutions to retain their highly skilled talent. Building a global leadership portfolio is the most scalable way to support operation teams and offer career mobility. Through leaders, manufacturers can execute change management and influence team environments, engagement and retention in global subsidiaries.
Operation leaders are task-oriented and don’t communicate well with their teams in high production environments. Which makes sense because they’re under extreme time and cost pressure to produce results and operate machinery.
Berend Kirch, L&D Consultant at Krauthammer
Therefore, upskilling managers at different seniority levels creates a pipeline of standard leadership skills at scale and supports talent promoted for their technical capabilities to develop beyond a first-time leadership role and ensure their skills stay in the company.
I often see managers that performed well in their specialty and therefore received a promotion, but they’re stuck between two jobs. They’re balancing their workload around 50/50 between their old role and their new leadership role. When manufacturers’ don’t invest in supporting them, this transition is quite draining.
Robert-Jan Stolk, L&D Comsultant at Krauthammer
Manufacturers must decrease their reliance on the external market
AI transformation promises new growth opportunities to manufacturers. However, new machinery and production methods will not deliver monetary and sustainability value on their own.
Manufacturers must source highly skilled talent to integrate, develop and maintain production technology. But sourcing this talent is the industry’s most concerning challenge. As a consequence, many companies are reliant on acquiring or employing technical specialists to execute their transformation.
However, the most successful manufacturers will decrease their reliance on the external market. They will internally develop highly skilled talent as well as create leadership pipelines for successful change management in global smart factories.
Download your guide for the manufacturing industry
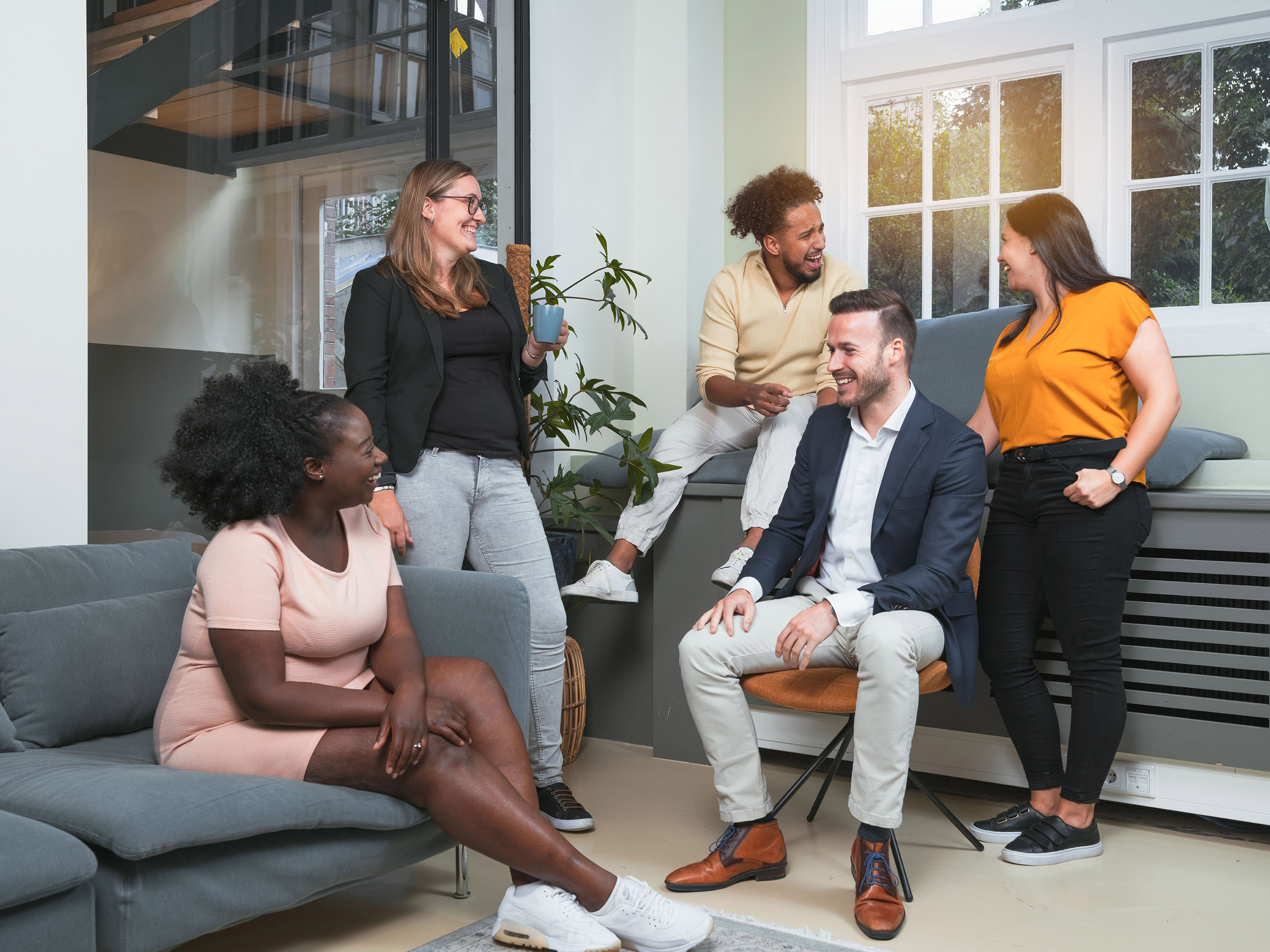
We offer a scalable employee training solution. It lets you continuously upskill your people.
Book a call.png)